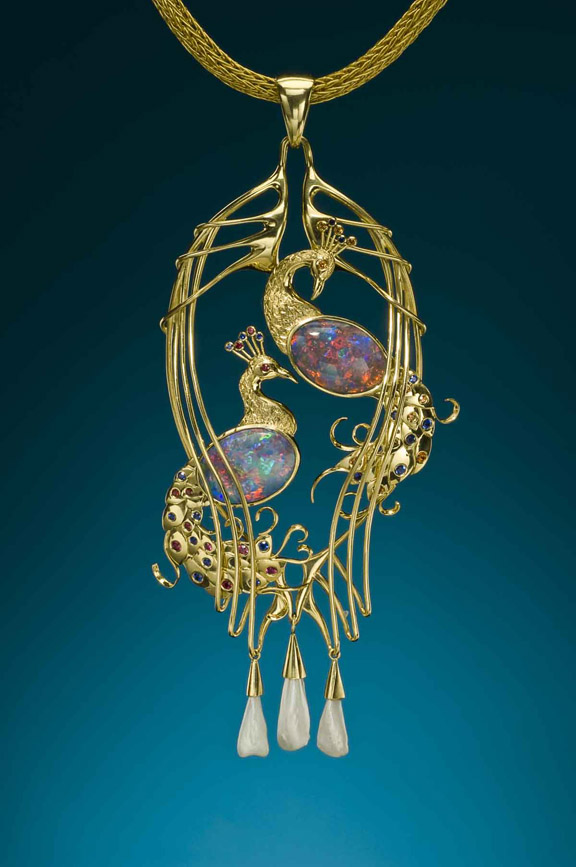
22k/18k hand fabricated Peacock Pendant. The piece is accented with two black opals from the Moonshine Field at Lightning Ridge as well as rubies, sapphires, natural Mississippi pearls and spessartite garnets. Designed and handmade by R. W. Wise, Goldsmiths, Michael Corneau, designer/craftsman.
by Richard W. Wise, G.G., A.S.G.
©2013 all rights reserved.
What is art and is the work of the goldsmith an art at all or merely a craft? This is an ancient debate. Some would argue that the use of precious materials, as opposed to more mundane materials, such as paint and canvas disqualifies the metalsmith and his product from the status and stature of the fine artist. Jewelry is all about the materials, gold, platinum, gemstones, design being viewed as a secondary concern. The objective of the goldsmith, is to decorate the body and decoration is not art.
That the piece pictured left is decorative cannot be denied. Its inspiration hails from the Art Nouveau Movement (1900-1910), with a design iconography that evolved out of the Arts & Crafts Movement, which paradoxically stressed the use of simple non-ostentatious materials and hand craftsmanship. Like Arts & Crafts jewelry, Art Nouveau jewelry utilized naturalistic design, but whereas Arts & Crafts practitioners emphasized the use of unusual and relatively mundane non-precious materials, Art Nouveau eschewed the ideological and abandoned the mundane but retained the emphasis on the naturalistic embracing a a more feminine, sensuous vocabulary partially through the use of precious materials.
It is no mistake that the Art Nouveau Period parallels what has become known as The Gilded Age—neither saw anything wrong for sumptuous decoration for its own sake. Plato reduced art to beauty. Is decoration art or is it something else, I guess you will have to decide.
As is often the case, we began with a client, a magnificent pair of black opals and an idea. We worked with the client over several months. The following images illustrate far better than any words the development of the concept.
Birth of A Concept:
The concept began with a pair of black opals the two peacocks, a perennial part of the Art Nouveau design lexicon. The peacock has been used as a symbol from the time of the ancient Greeks. However, in this case, it seemed particularly useful as a naturalistic excuse to show off the the bird’s plumage using a rainbow of colored gemstones.
Accenting Color
Finding accents for gem opal is always a challenge. Very few gemstones find a simpatico with opal. In this case; ruby and blue sapphire worked very well, picking up the corresponding hues in the opals, but when it came to the orange tones in the opal, orange sapphire and diamond simply did not work. The only gemstone that the opal would accept was spessartite garnet. Here is the preliminary
layout: In the next post, I’ll share some more images including the steps involved in the hand manufacture of this beautiful pendant. Stay tuned…